It's a bad idea to tune a harp using only numbers. The exact pitch of a single note played on a diatonic harmonica will vary by a few cents depending on a few things including your breath force, your embouchure and your attitude. So relying on numbers alone is very inaccurate.
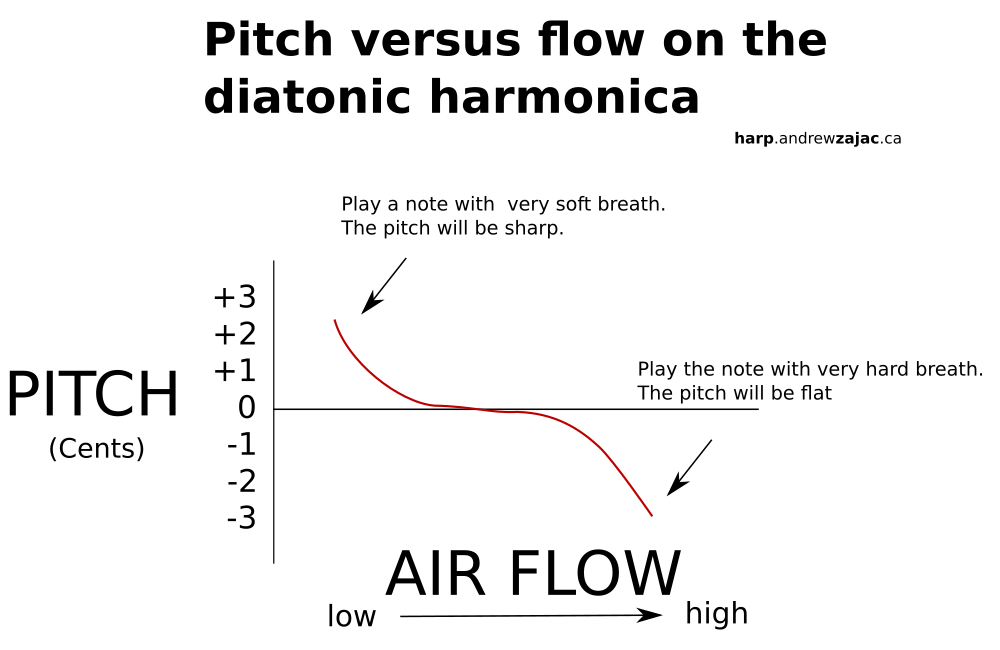
That being said, when you are tuning chords to sound in harmony, you need to know where approximately the pitch needs to be so that you can tune each reed to pair up with other reeds using your ears.
Some intervals are more important than others. When dealing with Standard Richter or altered tunings, here is a list of some of the intervals you will have to tune.
Sometime you will want to sacrifice harmony so that the single notes are in tune - this is a compromise as in "compromise tuning".
I can think of three things than help me decide whether to compromise or not:
1- How far away from ET you need to raise or lower the pitch.
2- How close to ET you or the person for whom you are tuning the harp would want each note to be.
3- How much the Just interval in question contributes to harmony (how good the interval sounds).
I have listed how important the harmony is for certain intervals so that it can help you decide which way to go on a case-by-case basis.
If the interval is not listed, don't worry about it and tune it close to ET. Its "Just" tuning doesn't provide any contribution to harmony to be of concern because these intervals will always sound dissonant.
Here is the Interval, the Ratio of the pitch of the tonic to the pitch of the interval, and the Offset which is plus or minus some cents from tuning it to zero on your tuner.
-----
Major second(*) - ratio 9:8. Its offset is about +4 cents.
This interval doesn't add very much to the harmony of the chord so don't worry too much about it. Six draw in Standard Richter is this interval. It's not too important relative to the tonic of the 1-2-3-4-5-6 draw chord (two draw) but it is relevant to the 4-5-6 chord which is a minor third. In that case, the 6 draw is a fifth of the tonic (four draw). Fifths on the other hand, are very important.
-----
Minor third - ratio 6:5. Its offset is about +16 cents.
A minor triad will still sound pretty strong even if the third is tuned to ET so this is not very important. It's a good place to compromise.
-----
Major third - ratio 5:4. Its offset is about -13 cents.
This interval is very important to a major triad. Try not to compromise with this interval.
-----
Fourth(*) - ratio 4:3. Its offset is about -2 cents.
A fourth is the same interval as a fifth but in the opposite direction. So try to not compromise here.
-----
Fifth(*) - ratio 3:2. Its offset is about +2 cents.
The Fifth implies the tonic. It is a very strong harmony when it is in tune. Try to not compromise here.
-----
Minor sixth - ratio 8/5. Its offset is about +13 cents.
This interval sounds good when in harmony. But I don't have a lot of experience with altered tunings using this interval.
-----
Major sixth - ratio 5:3. Its offset is about -16 cents.
This is used in Powerbender tuning on both the blow and draw plates and provides a very nice sounding interval. But -16 cents can sound pretty flat. Again, you choose as to whether you will use the interval or chord more than you want to keep the melody note in tune.
-----
Minor seventh - ratio 7:4. Its offset is about -30 cents.
This is the traditional sound of 7-Limit-Just Intonation tuning where in Standard Richter the 5 and 9 draw are tuned very flat. When in tune, playing any combination of draw holes together will imply the tonic note.
But -30 cents is too flat for melody notes to sound in tune. The usual compromise is to tune the 5 and 9 draw sharper and only play the 1-2-3-4 draw major chord excluding the 5.
-----
(*) A final note about Fifths, Fourths and Major Seconds (in standard Richter): Since these offsets are very close to ET - only within a few cents - you will not really have to compromise. But I suggest you focus on getting them accurately tuned; close isn't good enough! When these intervals are in harmony with the tonic, they will make that interval sound very very strong. But it has to be "bang-on" because the window of opportunity is small.
Even if you are only a fraction of a cent off, it's a missed opportunity to my ears...
-----
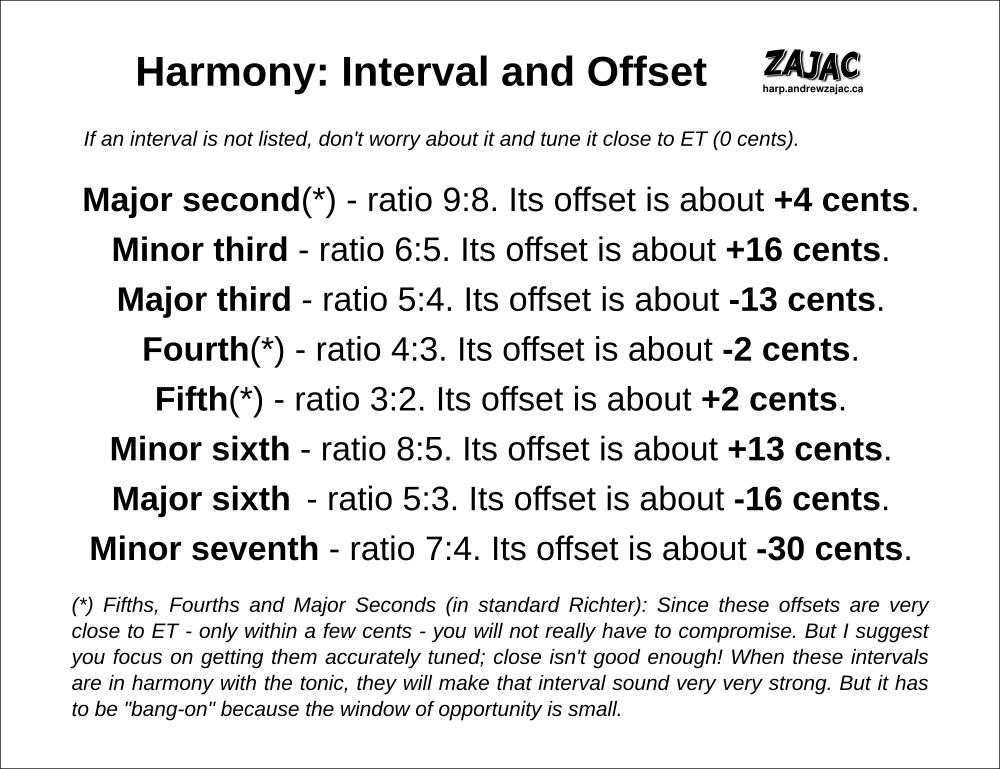
Are you new to tuning a diatonic harmonica? Here's a great place to start:
https://harp.andrewzajac.ca/Tune